The plan was simple: remove the front and rear transmission mounts (leaving a single mount on the passenger's side), lower the transmission like a lever until the motor was accessible through the driver's side wheel well, drill four holes, and put it all back.
The process involved breaking a half-inch socket extension and a Craftsman half-inch breaker bar. The ref called the fight at 8:45 on account of not having seen me all day.
Everything went smoothly enough at first. I had already removed the controller and the driver's side motor mount months ago. The rear tranny mount was connected to the top of the tranny and the top of a structural member going across the back of the engine compartment. If I disconnected it from the structural member, the tranny wouldn't be able to drop, because the mount would rest on the structure. Unfortunately, the bolts on top of the tranny were quite tight; I had to remove the batteries in the front rack to get a better angle.
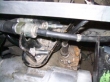
The rear mount also had mounts for two cables. I don't pretend to know what the cables are for. But they were ingeniously attached: each was keyed to fit in a fork, and the passenger side half was threaded. To remove them, I had to unscrew the threaded half part way, pull the cable away from the fork, and lift it out.
The front mount was connected to the front face of the tranny. It had to be completely disconnected and removed, mainly through brute force. Then I slowly lowered the jack.
That got about another inch, but not enough to work on the motor. The metal plate we used to mount the A/C compressor was rubbing against the motor and obstructing it.
I jacked the tranny back up and went to work on the A/C compressor plate. I had tried to move this last time, so the compressor was already off. I removed the two U-bolts that hold the plate to the front structural cross-member. Then I got underneath and pulled.
The condenser fan was preventing the metal plate from rotating far enough to come out. The contactor mounted on the plate wasn't helping much, either. I started loosening the condenser fan and the metal plate fell out, inches from my head.
Well, at least it was out. I started lowering again. The whole thing dropped with a crash. I got another inch or two, but still not enough to work on the motor. One of the bolts in the motor's brush end cap was resting on the front structural cross-member.
I didn't realize it at the time, but that meant the motor was slipping forwards as it dropped. I removed the nuts holding the brush bolt and pushed it into its bell housing. Then I carefully lowered the motor.
I got another six inches, but most of it was forwards. Why was the motor slipping forwards? Because the passenger axle's transmission end was stuck on the rear structural cross-member, I found. I needed to remove the passenger axle.
About this time, we took a break for lunch. It's near Melissa's birthday, and she chose to go to Amigo's. They gave her a big Mexican hat!
I got back and started trying to undo the passenger axle nut. It was significantly older-looking than the driver's site nut, and it was very well crimped. I used two different awls to uncrimp it, then used Nathan's 1-1/4" socket to pull it off.
Well, I tried to pull it off. It wouldn't come. I found a two-foot jack handle that would fit over my Craftsman 1/2" socket and tried again, with Melissa holding down the brakes. I needed an extension to get the handle past the wheel skirt, so I borrowed one of Nathan's.
I twisted the extension apart.
I called Nathan to deliver the bad news. He laughed, thank Heaven. He recommended I use one of his 1/2" breaker bars and a bigger lever. He said nothing I could do would break the breaker bar.
My garage is such a mess, it took me half an hour to find the breaker bar. Then I removed my four-foot jack handle, reversed it, and slipped the breaker bar in. Eri held the brakes while I pulled up. (Pushing down, I can't generate more force than my weight, unless I jump. Pulling up, I can generate LOTS of force.)
I heard a crackling noise and decided to stop. I found that I had twisted the chrome off the socket.
At this point I figured I might need to mangle the nut. I drove to the nearby auto stores, trying to find a new nut. I bought a new manual, since I had lost mine. It didn't say the nut was reverse threaded, so at least I hadn't been trying to tighten it accidentally.
But nobody had a new bolt. One of them told me I could get one with a new axle: $80. I started calling dealers, all of whom were closed, it being 5:45 by now. Eventually I found a new nut, at an Advance about 20 minutes away. I went and retrieved it, along with a black-wall socket. They assured me that this socket would not break.
So I gave it another try. Tatiana worked the brakes while I pushed up on the breaker bar. Suddenly, with a giant snap, something gave!
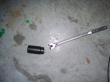
It was the breaker bar. Apparently I can generate much more force than Nathan thought.
At least I had a new bolt. That meant I could mangle the old one as much as necessary. With gleeful abandon I determined that much destruction would be necessary!
I tried my Dremel, but it didn't fit well, and barely left a mark. I switched to my cold chisels and started hammering away. I tried to leave the bolt in good enough condition to reattach the socket and try my hammer impact wrench every so often. My hands started hurting, so I found some gloves and continued slamming on the nut with my cold chisels.
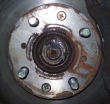
At 8:45, the bolt looked like the picture here, and Eri told me to come inside and help put the kids to sleep.
I had a nice shower. Tomorrow Nathan arrives at 8:00 AM. Perhaps he can make better progress than I did.